At first glance, PCB regardless of the intrinsic quality of how, on the surface are almost. It is through the surface that we can see the difference, and these differences are crucial to the durability and functionality of the PCB throughout its life.
Whether it is in the manufacturing process or in the actual use of the assembly process, PCB has a reliable performance, which is very important. In addition to the relevant costs, the assembly process of defects may be brought into the final product by PCB, in the actual use of the process may be faulty, resulting in claims. Therefore, from this point of view, can not be said, a high quality PCB costs are negligible.
In all segments of the market, especially the application of key products in the market, the failure consequences be unbearable to contemplate.
When comparing PCB prices, should bear in mind these aspects. Although reliable, there is a guarantee and long life products of higher costs, but in the long run or value for money.
High reliability of the circuit board of the 14 most important characteristics
25, 1 micron hole wall copper thickness
benefit
Enhanced reliability, including the ability to improve the expansion of the Z shaft.
The risk of not doing so
The electrical connectivity problems in the process of blowing holes or removing gas and assembling (inner layer separation, hole wall fracture), or in the actual use under the load conditions are likely to occur. IPCClass2 (most factories are used in the standard) provisions of the copper plating to be less 20%.
2, no welding repair or open repair
benefit
Perfect circuit to ensure reliability and safety, no maintenance, no risk
The risk of not doing so
If the repair is not properly, it will cause the circuit board circuit breaker. Even when it is properly repaired, there is a risk of failure in the load condition (vibration, etc.), which can be used in practice.
3, beyond the cleanliness requirements of the IPC specification
benefit
Improving the cleanliness of PCB can improve reliability.
The risk of not doing so
PCB residue, solder accumulation to anti welding layer risk and ionic residues will cause the weld surface corrosion and pollution risk, which may lead to reliability problems (bad solder joint / electrical fault), and finally to increase the probability of occurrence of actual fault.
4, strictly control the service life of each surface treatment
benefit
Solderability, reliability, and reduce the risk of moisture intrusion
The risk of not doing so
Due to the old circuit board surface treatment metallographic change may occur solder issue, and tidal intrusion may lead to layer, an inner layer and hole wall separation (break) etc. problems occurring in the assembly process and / or actual use in.
5, the use of internationally known substrate - not to use the "local" or unknown brand
benefit
Improve reliability and known performance
The risk of not doing so
Poor mechanical performance means that the circuit board can not play the expected performance under the assembly conditions, for example: high expansion performance will lead to delamination, break and warping problems. Weakening of electrical characteristics can lead to poor impedance performance.
6, copper clad plate tolerances meet IPC4101ClassB/L requirements
benefit
Strictly controlling the dielectric layer thickness can reduce the expected value of the electrical performance.
The risk of not doing so
Electrical performance may not be up to the requirements, the same batch of components in the output / performance will have a greater difference.
7, to define the resistance welding material, to ensure compliance with IPC-SM-840ClassT requirements
benefit
NCAB group recognized the "good" ink, to achieve the safety of ink, to ensure that the solder resist layer of ink in accordance with the UL standard.
The risk of not doing so
Can lead to inferior ink adhesion, resistance and hardness of flux. All of these problems can lead to the resistance of the solder layer and the circuit board, and ultimately lead to corrosion of copper circuit. Poor insulation performance can be caused by accidental electrical connectivity / arc caused by short circuit.
8, to define the shape, hole and other mechanical characteristics of tolerance
benefit
Strict control of the tolerances can improve the size and quality of the product - to improve the fit, shape and function
The risk of not doing so
Problems in the assembly process, such as alignment / alignment (only when the assembly is completed will find the problem of the press fit pin). In addition, due to the size deviation increases, into the base will be a problem.
9, NCAB specified solder resist layer thickness, although there is no relevant provisions of IPC
benefit
To improve the electrical insulation properties, reduce the risk of spalling or loss of adhesion, and strengthen the ability to fight against mechanical impact - no matter where the mechanical impact occurs!
The risk of not doing so
Resistance welding thin layer can lead to adhesion, resistance and hardness of flux. All of these problems can lead to the resistance of the solder layer and the circuit board, and ultimately lead to corrosion of copper circuit. The insulation property is not good due to the thin solder resist layer, which can lead to a short circuit due to the unexpected conduction / arc.
10, defined the appearance requirements and repair requirements, although IPC is not defined
benefit
Carefully cast in the process of manufacturing safety.
The risk of not doing so
A variety of scratches, minor damage, repair and repair - circuit boards can be used but not good-looking. In addition to the surface to see the problem, but also what can not see the risk, as well as the impact of assembly, and the actual use of the risk?
11, the hole depth requirement
benefit
High quality hole will reduce the risk of failure in the assembly process.With defects in need special assembly program, if not clearly marked scrap unit board (x-out), or not to it from the set in isolation, may be assembled this known bad board, parts and time can be wasted.
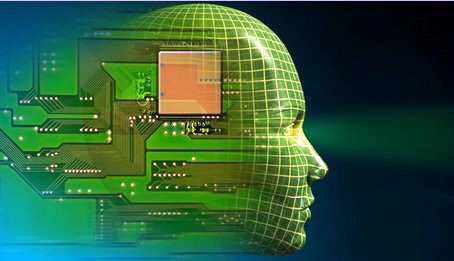